FD-200R Freeze Dryer
2000Kgs Industrial Food Freeze Dryer
The Vikumer FD-200R is our largest food freeze drying equipment, an industrial freeze dryer with 2000kgs batch loading. There are 4 modules of shelves offer total 204 sq.m useable product loading area. As well as the highly efficiency evapor collect condenser that can trap Total 4000kgs water. Users also can parallel several sets FD-200R to get a larger daily processing volume.
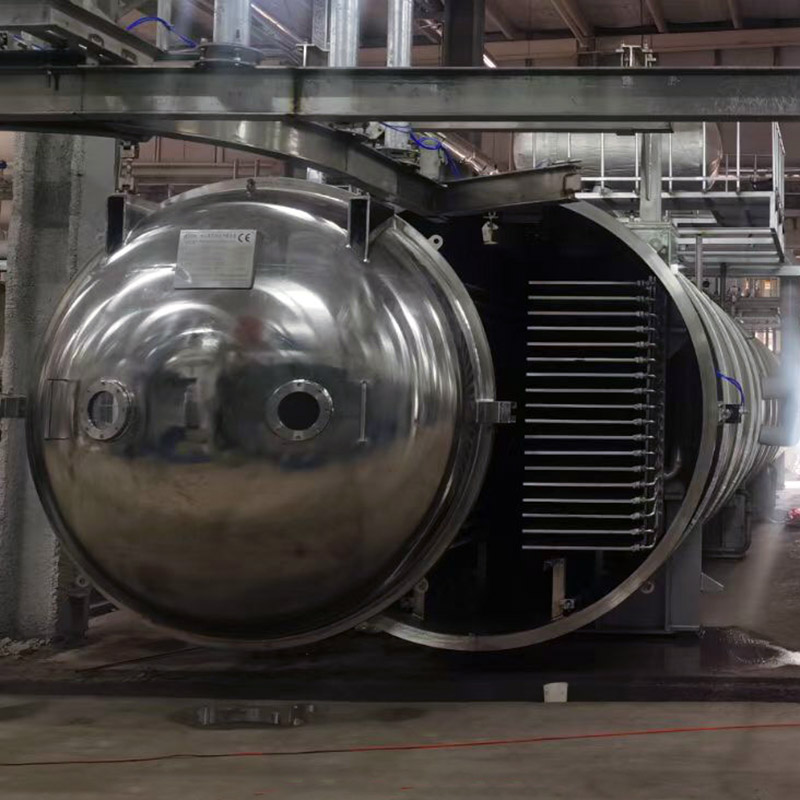
Technical Parameters
Model | FD-200R |
---|---|
Shelf Area | 204m2 |
Shelves | 4 modules, 17+1 each, mirror install in chamber |
Shelf Size | 630*5100mm |
Shelf Spacing | 100mm |
Shelf Temp. | RT ~ +100C |
Vacuum | <15Pa |
Condenser Capacity | 2000Kgs/24Hrs, 4000Kgs in total |
Condenser Temp. | -45C |
Power | 400Kwh |
Install Area | 25*15*4.5 meters |